Introduction to Reverse Engineering
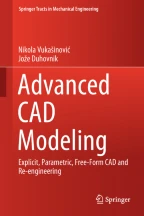
Reverse engineering has been practised since the beginning of technology. Fundamentally, it is about the identification of existing technical and natural solutions, and their reconstruction into new, identical or even improved technical solutions. Over the years it has flourished systematically, thanks to the development of new and technologically increasingly advanced and economically affordable measuring procedures, which allows the accurate reconstruction of not only technical principles but also detailed shapes and dimensions. This chapter explains the position of reverse engineering in the modern design and development process. It also introduces the main measuring methods for capturing data on the geometry of physical objects. These methods are divided into groups, depending on how they work and the physical laws on which they are based. We also present the main advantages and disadvantages of particular groups of methods, and recommendations for their application where the best results can be achieved.
This is a preview of subscription content, log in via an institution to check access.
Access this chapter
Subscribe and save
Springer+ Basic
€32.70 /Month
- Get 10 units per month
- Download Article/Chapter or eBook
- 1 Unit = 1 Article or 1 Chapter
- Cancel anytime
Buy Now
Price includes VAT (France)
eBook EUR 106.99 Price includes VAT (France)
Hardcover Book EUR 137.14 Price includes VAT (France)
Tax calculation will be finalised at checkout
Purchases are for personal use only
References
- Kai CC, Meng CS, Ching LS et al (2000) Facial prosthetic model fabrication using rapid prototyping tools. Integr Manufact Syst 11(1):42–53. https://doi.org/10.1108/09576060010303668ArticleGoogle Scholar
- Duhovnik J, Kljajin M, Opalić M (2009) Inženirska grafika. Fakulteta za strojništvo, Ljubljana Google Scholar
- Kusnoto B, Evans CA (2002) Realibility of a 3d surface laser scanner for orthodontic applications. Am J Orthod Dentofac Orthop 122:342–348. https://doi.org/10.1067/mod.2002.128219ArticleGoogle Scholar
- Thali MJ, Braun M, Dirnhofer R (2003) Optical 3d surface digitizing in forensic medicine: 3d documentation of skin and bone injuries. Forensic Sci Int 137:203–208. https://doi.org/10.1016/j.forsciint.2003.07.009ArticleGoogle Scholar
- Chua CK, Chou SM, Ng WS et al (1998) An integrated experimental approach to link a laser digitiser a CAD/CAM system and a rapid prototyping system for biomedical applications. Int J Adv Manufact Technol 14:110–115. https://doi.org/10.1007/BF01322219ArticleGoogle Scholar
- Bradshaw G, Moss R (1999) Towards a prototype for the collection of digital medieval moulding profiles. In: Proceedings of the fifteenth annual CHArt conference held at the University of Glasgow Google Scholar
- Bernard A, Laroche F, Ammar-Khodja S, Perry N (2007) Impact of new 3D numerical devices and environments on redesign and valorisation of mechanical systems. Ann CIRP Manufact Technol 56(1):143–148. https://doi.org/10.1016/j.cirp.2007.05.035ArticleGoogle Scholar
- Pieraccini M, Guidi G, Atzeni C (2001) 3D digitizing of cultural heritage. J Cult Heritage 2:63–70. https://doi.org/10.1016/S1296-2074(01)01108-6ArticleGoogle Scholar
- Chow S-K, Chan K-L (2009) Reconstruction of photorealistic 3D model of ceramic artefacts for interactive virtual exhibition. J Cult Heritage 10:161–173. https://doi.org/10.1016/j.culher.2008.08.011ArticleGoogle Scholar
- Vacharanukul K, Mekid S (2005) In-process dimensional inspection sensors. Measurement 38:204–218. https://doi.org/10.1016/j.measurement.2005.07.009ArticleGoogle Scholar
- Lee KH, Park H, Son S (2001) A framework for laser scan planning of freeform surfaces. Int J Adv Manufact Technol 17:171–180. https://doi.org/10.1007/s001700170187ArticleGoogle Scholar
- Son S, Kim S, Lee KH (2003) Path planning of multi-patched freeform surfaces for laser scanning. Int J Adv Manufact Technol 22:424–435. https://doi.org/10.1007/s00170-002-1502-0ArticleGoogle Scholar
- Vukašinović N, Bračun D, Možina J, Duhovnik J (2010) The influence of incident angle, object colour and distance on CNC laser scanning. Int J Adv Manufact Technol 50:265–274. https://doi.org/10.1007/s00170-009-2493-xArticleGoogle Scholar
- Vukašinović N, Korošec M, Duhovnik J (2010) The influence of surface topology on the accuracy of laser triangulation scanning results = vpliv topologije površine na natančnost meritev z laserskim triangulacijskim merilnikom oblike površin. Strojniški vestnik 56(1):23–30 ArticleGoogle Scholar
- Vukašinović N, Bračun D, Možina J, Duhovnik J (2012) A new method for defining the measurement uncertainty model of CNC laser-triangulation scanner. Int J Adv Manufact Technol 58(9):1097–1104. https://doi.org/10.1007/s00170-011-3467-3ArticleGoogle Scholar
- Vukašinović N, Možina J, Duhovnik J (2012) Correlation between incident angle, measurement distance, object colour and the number of acquired points at CNC laser scanning. Strojniški vestnik 58(1):23–28. https://doi.org/10.5545/sv-jme.2011.053ArticleGoogle Scholar
- Duhovnik J, Balić S (2004) Detail functionality analysis using the design golden loop. In: Proceeding of the conference, EDIProD’2004, Zielona Gora Google Scholar
- Son S, Park H, Lee KH (2002) Automated laser scanning system for reverse engineering and inspection. Int J Mach Tools Manuf 42:889–897. https://doi.org/10.1016/S0890-6955(02)00030-5ArticleGoogle Scholar
- Chang C-C, Li Z, Cai X, Dempsey P (2007) Error control and calibration in three-dimensional anthropometric measurement of the hand by laser scanning with glass support. Measurement 40:21–27. https://doi.org/10.1016/j.measurement.2006.05.006ArticleGoogle Scholar
- Martinez S, Cuesta E, Barriero J, Alvarez B (2010) Analysis of laser scanning and strategies for dimensional and geometrical control. Int J Adv Manufact Technol 46(5–8):621–629. https://doi.org/10.1007/s00170-009-2106-8ArticleGoogle Scholar
- Wang G-J, Wang C-C, Chuang SHF (1999) Reverse engineering of sculptured surfaces by four-axis non-contacting scanning. Int J Adv Manufact Technol 15(11):800–809. https://doi.org/10.1007/s001700050135ArticleGoogle Scholar
- Page D, Koschan A, Sun Y, Abidi M (2003) Laser-based imaging for reverse engineering. Sens Rev Special Issue Mach Vis Laser Scanners 23(3):223–229 Google Scholar
- Yao AWL (2005) Applications of 3D scanning and reverse engineering techniques for quality control of quick response products. Int J Adv Manufact Technol 26:1284–1288. https://doi.org/10.1007/s00170-004-2116-5ArticleGoogle Scholar
- Willis A, Speicher J, Cooper DB (2007) Rapid prototyping 3D objects from scanned measurement data. Image Vis Comput 25:1174–1184. https://doi.org/10.1016/j.imavis.2006.06.011ArticleGoogle Scholar
- Soković M, Kopač J (2006) RE (reverse engineering) as necessary phase by rapid product development. Int J Mach Tools Manuf 175:398–403. https://doi.org/10.1016/j.jmatprotec.2005.04.047ArticleGoogle Scholar
- Vukašinović N, Kolšek T, Duhovnik J (2007) Case study—surface reconstruction from point clouds for prosthesis production. J Eng Des 18(5):475–488. https://doi.org/10.1080/09544820701403805ArticleGoogle Scholar
- Budak I, Hodolić J, Soković M (2005) Development of a programme system for data-point preprocessing in reverse engineering. J Mater Process Technol 162–163:730–735. https://doi.org/10.1016/j.jmatprotec.2005.02.214ArticleGoogle Scholar
- Budak I, Soković M, and Hodolić J (2007) Implementation of innovative procedure for error estimation in cross-sectional data-point reduction in reverse engineering. Int J Total Qual Manag Excellence 35(1–2) Google Scholar
- Bračun D, Gruden V, Možina J (2008) A method for surface quality assessment of die-castings based on laser triangulation. Meas Sci Technol 19:1–8. https://doi.org/10.1088/0957-0233/19/4/045707ArticleGoogle Scholar
- Shiou FJ, Pfeifer T (2002) Strategies and processes to measure the dimensional geometry of sheet metal parts for exact laser cutting. Int J Adv Manufact Technol 15:800–809 Google Scholar
- Shiou FJ, Chen M-J (2003) Intermittent process measurement of a freeform surface profile with circular triangulation laser probe on a machining centre. Int J Adv Manufact Technol 21:365–376. https://doi.org/10.1007/s001700300042ArticleGoogle Scholar
- Li Y, Gu P (2004) Free-form surface inspection techniques state of the art review. Comput Aided Des 36:1395–1417. https://doi.org/10.1016/j.cad.2004.02.009ArticleMathSciNetGoogle Scholar
- Zexiao X, Jianguo W, Quimei Z (2005) Complete 3D measurement in reverse engineering using a multi-probe system. Int J Mach Tools Manuf 45:1474–1486. https://doi.org/10.1016/j.ijmachtools.2005.01.028ArticleGoogle Scholar
- Shiou FJ, Ali YC (2005) Development of a non-contact multi-axis reverse engineering measurement system for small complex objects. In: Publishing Journal of Physics: Conference Series 13, 7th international symposium on measurement technology and intelligent instruments, pp 419–425 Google Scholar
- Fan KC (1997) A non-contact automatic measurement for free-form surface profiles. Comput Integr Manufact Syst 10(4):277–285. https://doi.org/10.1016/S0951-5240(97)00020-7ArticleGoogle Scholar
- Zexiao X, Quimei Z, Guoxiong Z (2004) Modelling and calibration of a structured-light-sensor-based five-axis scanning system. Measurement 36:185–194. https://doi.org/10.1016/j.measurement.2004.05.003ArticleGoogle Scholar
- Zexiao X, Chengguo Z, Quimei Z, Guoxiong Z (2005) Modelling and verification of a five-axis laser scanning system. Int J Adv Manufact Technol 26:391–398. https://doi.org/10.1007/s00170-004-2106-7ArticleGoogle Scholar
- Huang SJ, Lin CC (1997) A three-dimensional non-contact measuring system. Int J Adv Manufact Technol 13:419–425. https://doi.org/10.1007/BF01179037ArticleGoogle Scholar
Author information
Authors and Affiliations
- University of Ljubljana, Ljubljana, Slovenia Nikola Vukašinović & Jože Duhovnik
- Nikola Vukašinović